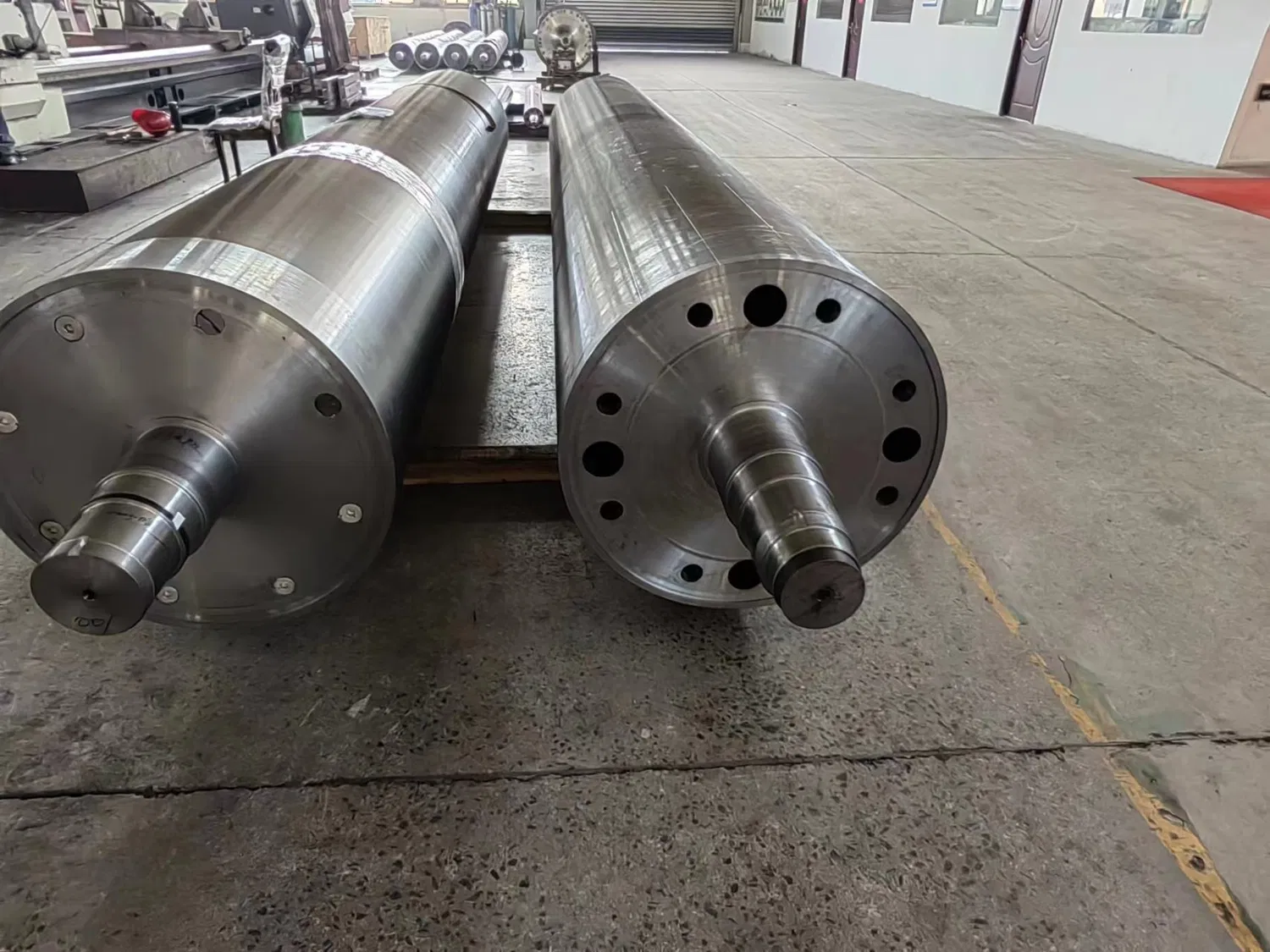
Roller compaction, also known as dry granulation, is a critical process in pharmaceutical, chemical, and food industries. It involves compacting powder materials between two counter-rotating rollers to create a continuous sheet or ribbon, which is subsequently milled into granules. But what are the different types of roller compaction available, and which one is right for your specific needs? This article will explore the various roller compactor designs, their applications, and key factors to consider when choosing the optimal equipment.
Horizontal Roller Compactors
Horizontal roller compactors are the most common type used in the industry. They feature two horizontally oriented rollers that rotate in opposite directions, compressing the powder fed between them. These compactors are known for their high throughput, robust design, and ability to handle a wide range of materials. Within this category, you'll find variations such as standard horizontal roller compactors and integrated horizontal roller compactors, which combine the compaction and milling processes into a single unit. This streamlined approach can improve efficiency and reduce material handling.
Vertical Roller Compactors
Vertical roller compactors, while less common than their horizontal counterparts, offer distinct advantages for certain applications. In these systems, the rollers are positioned vertically, with the powder fed from above. This configuration allows for a smaller footprint and can be beneficial for processing cohesive or difficult-to-feed materials. Gravity assists the feeding process, minimizing the risk of bridging or rat holing in the feed hopper. However, vertical roller compactors typically have a lower throughput compared to horizontal designs.
Sphere Roller Compactors
Sphere roller compactors represent a newer technology in roller compaction. Instead of cylindrical rollers, they utilize spherical rollers to compact the powder. This unique design creates a more uniform pressure distribution across the powder bed, leading to improved granule consistency and higher compaction efficiency. Sphere roller compactors also offer better control over granule size and density, making them suitable for specialized applications requiring precise particle characteristics.
Choosing the Right Roller Compactor
Selecting the appropriate roller compactor involves careful consideration of several factors. The characteristics of the powder being processed, including particle size distribution, flowability, and compressibility, play a crucial role. The desired throughput, granule properties, and budget constraints also influence the decision-making process. So, how do you choose the best option? Consider consulting with experts in roller compaction technology to determine the most suitable type for your specific application.
Optimizing Roller Compaction Performance
Achieving optimal performance with roller compaction requires more than just selecting the right equipment. Process parameters, such as roller speed, gap, and feed rate, need to be carefully controlled to ensure consistent granule quality. Monitoring and adjusting these parameters based on real-time data can significantly improve efficiency and minimize variability. What are some strategies for optimizing these parameters? Experimentation and careful analysis of the resulting granules are essential for fine-tuning the process.
Applications of Roller Compaction
Roller compaction finds wide-ranging applications across various industries. In pharmaceuticals, it's commonly used for improving the flow properties of powders for tablet compression and capsule filling. In the chemical industry, roller compaction is employed for granulating fertilizers, pesticides, and other chemical products. The food industry utilizes this technology for processing ingredients like powdered milk, sugar, and spices. The versatility of roller compaction makes it a valuable tool for diverse manufacturing processes.
Advantages of Roller Compaction
Roller compaction offers numerous advantages compared to other granulation methods. It's a dry process, eliminating the need for solvents or drying steps, which can simplify manufacturing and reduce costs. It also improves powder flow, reduces dust generation, and enhances the uniformity of blends. These benefits contribute to increased productivity, improved product quality, and a safer working environment.
Roller Compaction vs. Other Granulation Techniques
While roller compaction is a highly effective granulation method, other techniques like wet granulation and fluid bed granulation exist. Each method has its own advantages and disadvantages, making it crucial to select the most appropriate technique based on the specific application. Wet granulation, for instance, is suitable for moisture-sensitive materials, whereas fluid bed granulation offers excellent control over granule size and morphology. Understanding the differences between these methods allows for informed decision-making and optimal process selection.
Future Trends in Roller Compaction
The field of roller compaction continues to evolve, with ongoing research and development focused on improving efficiency, control, and versatility. Emerging technologies like continuous manufacturing and process analytical technology (PAT) are being integrated with roller compaction to enhance process understanding and optimize performance. These advancements promise to further solidify roller compaction's role as a key technology in various industrial applications.
Conclusion: Making Informed Decisions about Roller Compaction
Understanding the different types of roller compaction and their applications is crucial for achieving optimal manufacturing outcomes. Whether you're looking to improve powder flow, enhance granule consistency, or streamline your production process, choosing the right roller compactor is essential. By considering the factors discussed in this article and seeking expert advice when needed, you can leverage the power of roller compaction to enhance your manufacturing processes. For further assistance, consider contacting equipment manufacturers or consulting with specialists in powder processing technologies. They can provide tailored recommendations and support for implementing roller compaction effectively.