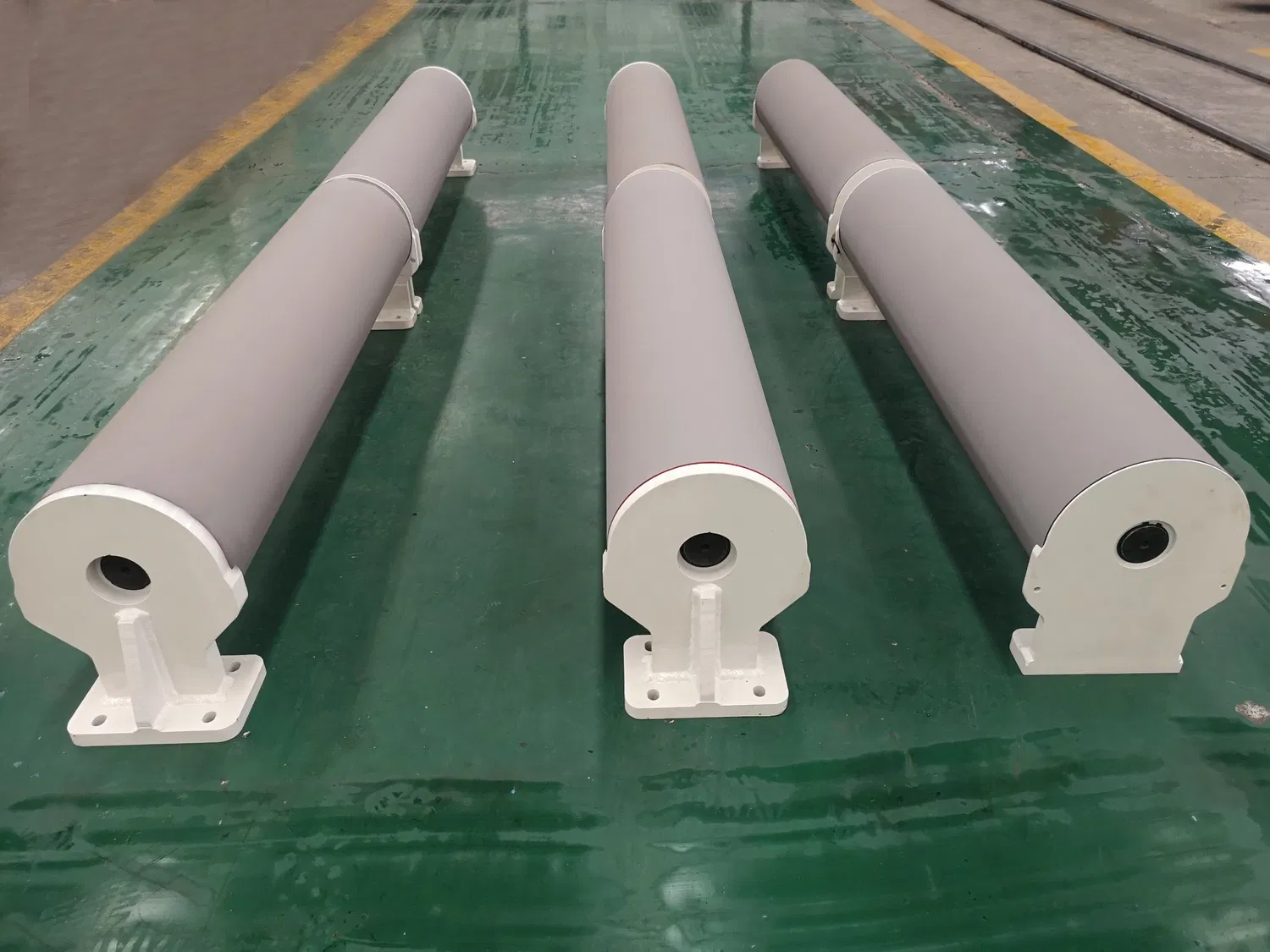
Nip mechanics plays a crucial role in determining the final properties of paper, influencing everything from smoothness and thickness to strength and printability. Understanding this complex interplay of forces within the paper machine is key to optimizing both product quality and production efficiency. This article delves into the core principles of nip mechanics, offering insights into how these principles can be applied for practical improvements in papermaking.
The Fundamentals of Nip Pressure
At its core, the nip is the region where two rolls come into contact under pressure, creating a zone of intense force that acts upon the paper web. This nip pressure is the primary driving force behind several crucial processes, including water removal in the press section, consolidation of the paper sheet, and surface modification in the calendering process. Controlling and manipulating this pressure is essential for achieving desired paper characteristics.
The Influence of Temperature and Speed
While nip pressure is a central factor, temperature and speed also play significant roles in the nip mechanics equation. Increased temperature can soften the paper web, allowing for greater conformability and improved bonding within the sheet. Speed, on the other hand, affects the dwell time of the paper within the nip, influencing the effectiveness of both pressing and calendering operations. The interplay of these three factors – pressure, temperature, and speed – creates a complex dynamic that demands careful consideration.
Optimizing Nip Mechanics in the Press Section
The press section of a paper machine utilizes nip mechanics to remove water from the paper web after it leaves the forming section. Effective water removal in the press section is critical for energy efficiency, as it reduces the amount of drying required later in the process. Optimizing nip pressure, along with felt properties and roll design, is essential for maximizing water removal while minimizing sheet damage. But how do you strike the perfect balance between aggressive pressing for efficiency and gentle handling to preserve sheet integrity?
Calendering and the Refinement of Paper Properties
Further down the line, calendering utilizes nip mechanics to refine the surface properties of the paper. By passing the paper through a stack of calender rolls, the surface smoothness, gloss, and printability can be significantly enhanced. Precise control of nip pressure and temperature in the calender stack is paramount for achieving the desired surface finish without compromising the bulk and strength of the paper.
The Role of Materials and Roll Coverings
The materials used for roll coverings also play a vital role in nip mechanics. Different materials offer varying degrees of hardness, resilience, and surface texture, each influencing the way the nip interacts with the paper web. Choosing the appropriate roll covering material for a specific application is essential for optimizing nip performance and achieving the desired paper properties.
Advanced Technologies in Nip Mechanics
Recent advancements in nip mechanics involve the use of sensors and control systems to monitor and adjust nip pressure in real-time. These technologies allow for more precise control of the papermaking process, leading to improved product quality and consistency. Imagine the possibilities of a fully automated system, constantly adjusting nip parameters based on real-time feedback – this is the future of papermaking.
Troubleshooting Common Nip-Related Issues
Common problems related to nip mechanics include sheet breaks, uneven caliper, and surface defects. Understanding the root causes of these issues is crucial for implementing effective solutions. Factors such as improper nip pressure, uneven roll surfaces, or incorrect roll alignment can all contribute to these problems.
Practical Tips for Improved Nip Performance
So, how can you improve your nip performance in practice? Regular maintenance and inspection of rolls, careful control of nip pressure and temperature, and selection of appropriate roll coverings are all key steps. Furthermore, staying updated on the latest advancements in nip technology can provide valuable insights for optimizing your papermaking process.
The Future of Nip Mechanics in Papermaking
The science of nip mechanics continues to evolve, driven by the demand for higher quality paper products and increased production efficiency. Ongoing research and development efforts are focused on further refining our understanding of the complex interactions within the nip, paving the way for even greater control and optimization of the papermaking process. What new innovations will shape the future of nip mechanics? This is an exciting area to watch.
Do you have any experiences with optimizing nip mechanics in your papermaking operations? Share your thoughts and insights in the comments below. For further assistance with optimizing your papermaking process, contact our team of experts.