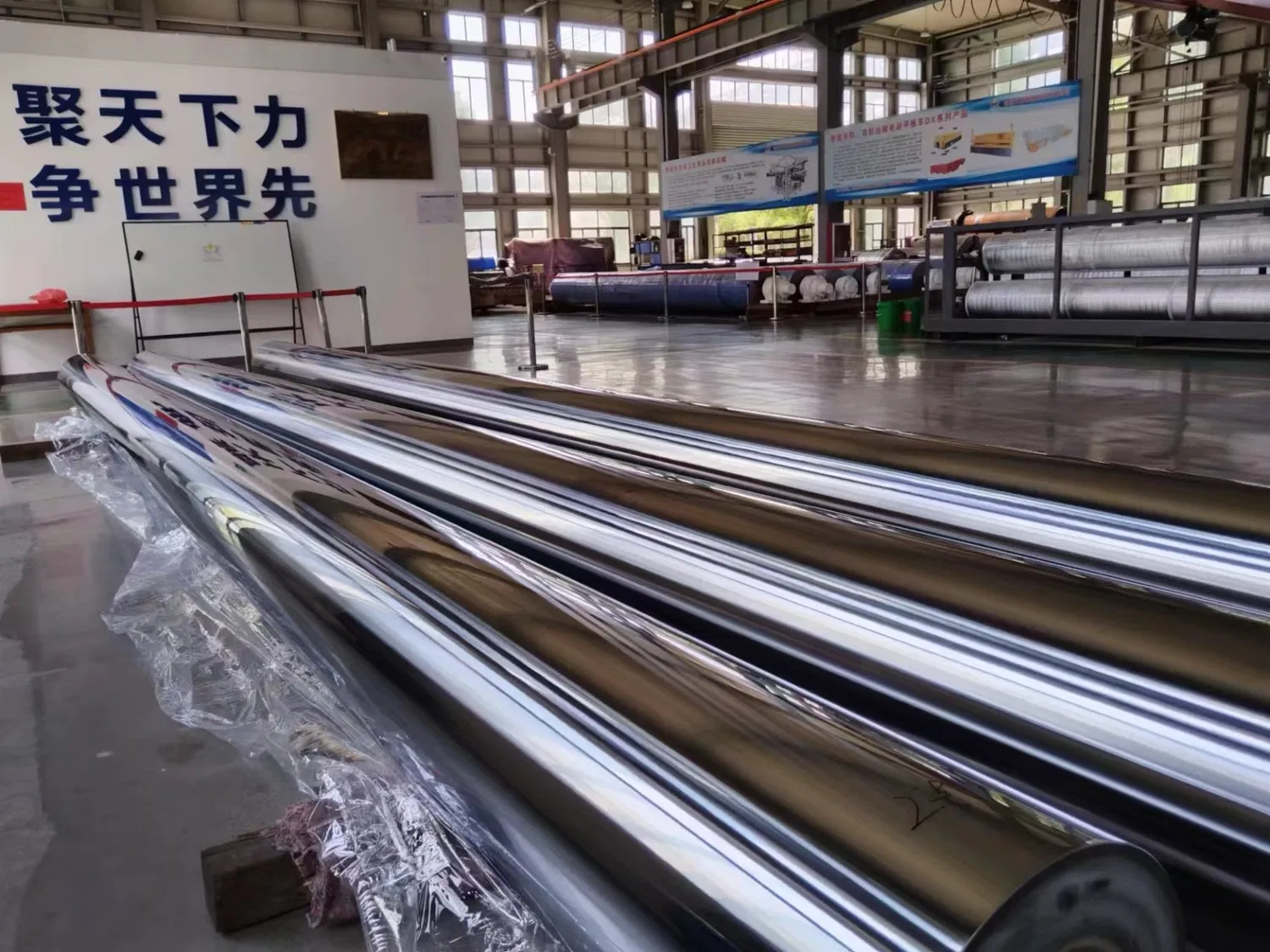
Optimizing roll loading and pressure distribution is critical for achieving consistent product quality, minimizing waste, and maximizing the lifespan of your rolls. Whether you're working with paper, film, foil, or other web materials, understanding the forces at play within your roll system is essential. This article will explore the key factors influencing roll loading and pressure distribution, providing actionable strategies for optimization.
Understanding the Basics of Roll Loading
Roll loading refers to the forces acting upon a roll, including the weight of the roll itself, the tension of the web material passing over it, and any external applied forces. These forces influence the pressure distribution across the roll face, which directly impacts the web's properties and the overall process efficiency. Uneven pressure distribution can lead to issues like wrinkles, bagging, and variations in thickness or density.
Factors Affecting Pressure Distribution
Several factors contribute to the pressure distribution profile across a roll. Roll cover hardness, roll diameter, and the web material's properties all play significant roles. Furthermore, the nip pressure – the force exerted between two rolls in contact – is a critical parameter affecting pressure distribution and ultimately, product quality. Are you considering the impact of these individual elements on your process?
Optimizing Roll Coverings for Enhanced Performance
Selecting the appropriate roll covering material is crucial for optimizing pressure distribution. Different materials exhibit varying hardness, resilience, and friction coefficients. Choosing the right covering for your specific application can significantly improve web handling, minimize wear, and enhance the overall efficiency of your process. For instance, softer covers can conform better to irregularities in the web, while harder covers offer greater durability and resistance to wear.
The Importance of Proper Roll Alignment
Accurate roll alignment is essential for ensuring even pressure distribution and preventing issues like web wander and uneven wear. Misaligned rolls can lead to localized high-pressure zones, causing premature roll wear and defects in the processed material. Regular inspection and adjustment of roll alignment are crucial for maintaining optimal performance.
Techniques for Measuring and Monitoring Pressure Distribution
Several techniques can be employed to measure and monitor pressure distribution across the roll face. Pressure mapping sensors provide detailed information about the pressure profile, enabling precise adjustments to roll loading and alignment. These measurements can be invaluable for troubleshooting issues and optimizing the overall process.
Practical Tips for Optimizing Roll Loading and Pressure Distribution
Implementing these practical tips can help you achieve optimal roll loading and pressure distribution:
* **Regularly inspect and clean rolls:** This prevents the buildup of debris that can affect pressure distribution.
* **Ensure proper web tension control:** Maintaining consistent web tension is essential for uniform pressure distribution.
* **Optimize nip pressure:** Experimenting with different nip pressures can help you find the sweet spot for your specific application.
* **Consider crowned rolls:** Crowned rolls are designed with a slightly larger diameter in the center, helping to compensate for deflection under load and promote even pressure distribution.
Troubleshooting Common Roll Loading Issues
Common roll loading issues include uneven pressure distribution, excessive roll wear, and web wrinkles. By understanding the underlying causes of these problems, you can implement effective solutions. For example, uneven wear might indicate a misalignment issue, while wrinkles could be caused by improper web tension or roll cover selection. How are you currently addressing these challenges in your operations?
Advanced Techniques: Finite Element Analysis (FEA) for Roll Optimization
For complex applications, Finite Element Analysis (FEA) can provide detailed insights into roll loading and pressure distribution. FEA simulations can predict how different parameters will affect roll performance, allowing for virtual optimization before implementing changes in the real world. This can save significant time and resources in the long run.
Conclusion: Achieving Optimal Roll Performance Through Careful Optimization
Optimizing roll loading and pressure distribution is a continuous process requiring careful attention to detail. By understanding the key factors influencing roll performance and implementing the strategies outlined in this article, you can achieve consistent product quality, minimize waste, and extend the lifespan of your rolls. Consider conducting a thorough assessment of your current roll system and identify areas for improvement. Implementing even small changes can lead to significant gains in efficiency and performance. Remember, consistent monitoring and adjustment are essential for maintaining optimal roll performance over time.