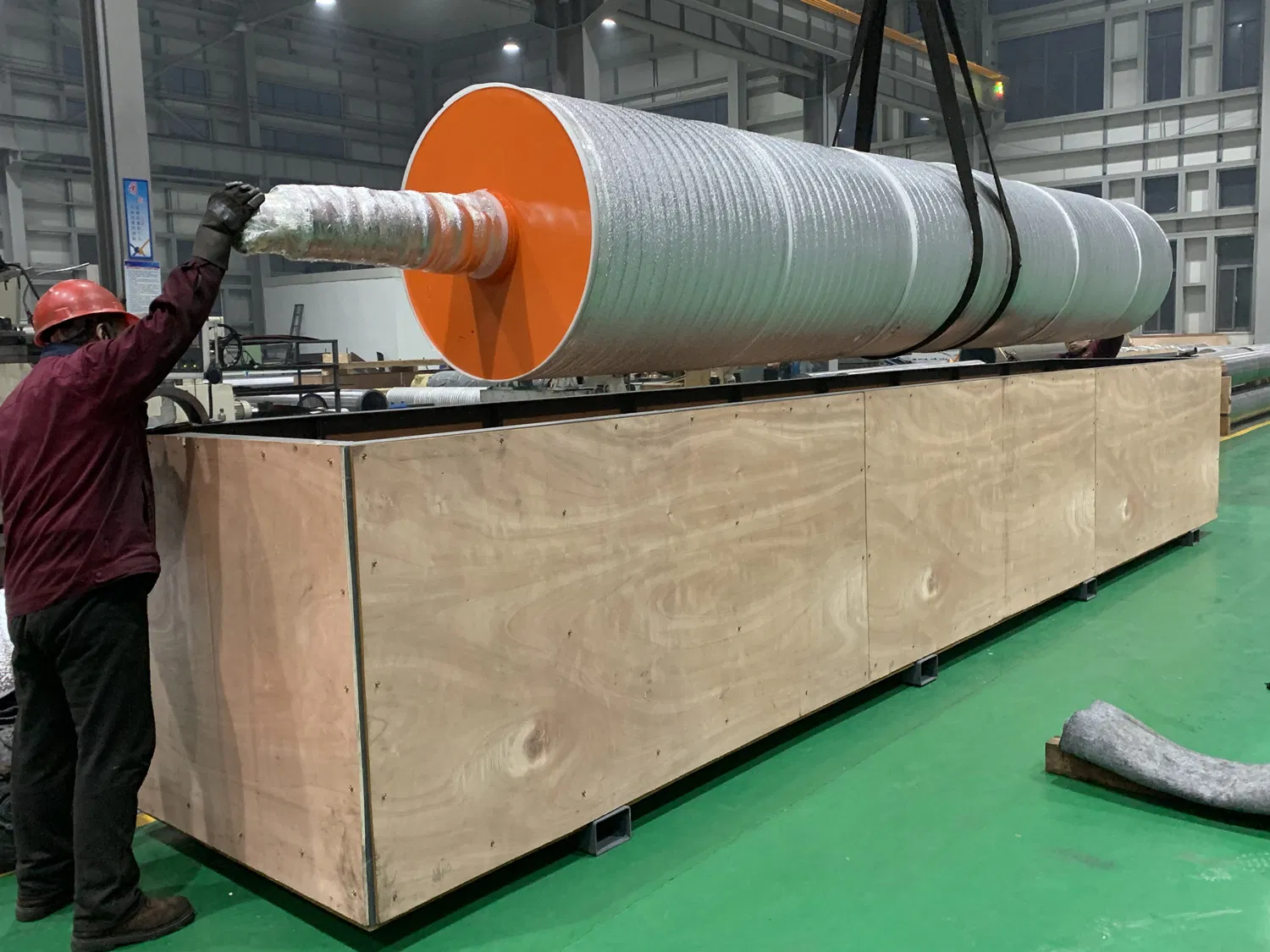
Roll crown control is a critical aspect of papermaking that significantly influences the final product's quality and the overall efficiency of the production process. It refers to the management of the roll's cross-machine profile, ensuring uniform pressure distribution across the entire width of the paper web during processes like calendering. Without effective roll crown control, paper manufacturers face issues like uneven caliper, wrinkles, and baggy edges, ultimately leading to increased waste and reduced profitability.
Understanding the Impact of Roll Crown
The crown of a roll is the slight curvature engineered into its surface. This intentional curvature compensates for the deflection that occurs under load during papermaking operations. Without this compensation, the center of the roll would exert more pressure than the edges, leading to uneven caliper and potential defects.
Common Problems Caused by Ineffective Roll Crown Control
Ineffective roll crown control can lead to a range of problems, including uneven caliper across the web, wrinkles, baggy edges, and difficulties in maintaining consistent moisture profiles. These issues not only compromise the quality of the finished paper but also increase waste and downtime. For example, wrinkles can cause web breaks, leading to costly production interruptions and wasted resources.
Calendering and the Role of Roll Crown
Calendering, a critical stage in papermaking, heavily relies on precise roll crown control. This process involves passing the paper web through a stack of rollers (calender rolls) under pressure to achieve the desired smoothness and gloss. Proper roll crown control in calendering is crucial for ensuring uniform pressure distribution across the nip, which directly impacts the final paper properties. Inconsistent nip pressure can result in an uneven finish, affecting the paper's printability and overall quality.
Techniques for Achieving Effective Roll Crown Control
Several techniques are employed to achieve effective roll crown control. These include:
* **Controlled crowning:** This involves grinding a specific crown profile onto the roll surface during manufacturing.
* **Thermal crowning:** This method utilizes controlled heating and cooling of the roll to influence its shape and achieve the desired crown.
* **Bending compensation:** This technique involves applying external forces to the roll to counteract deflection and maintain a uniform nip pressure.
Implementing Best Practices for Roll Crown Management
Implementing best practices for roll crown management is essential for maximizing paper quality and production efficiency. This involves regular inspection and measurement of roll crowns, meticulous record-keeping, and proactive adjustments based on operational data. Furthermore, understanding the specific requirements of different paper grades and adjusting the roll crown accordingly is crucial for optimal performance.
Advanced Technologies in Roll Crown Control
Recent advancements in roll crown control technology include automated systems that monitor and adjust the roll crown in real-time. These systems utilize sensors and sophisticated control algorithms to maintain optimal nip pressure, minimizing variations and improving consistency. These technologies contribute significantly to reducing waste, increasing productivity, and enhancing the overall quality of the paper produced. But how do you choose the right technology for your specific needs?
Choosing the Right Roll Crown Control Strategy
Selecting the appropriate roll crown control strategy depends on various factors, including the specific paper grade being produced, the calendering configuration, and the overall production environment. Consulting with experienced roll manufacturers and control system specialists can provide valuable insights and guidance in choosing the most effective solution.
The Benefits of Optimized Roll Crown Control in Papermaking
The advantages of optimized roll crown control are numerous and contribute to a more efficient and profitable papermaking operation. These benefits include improved paper quality, reduced waste, increased productivity, and lower energy consumption. By ensuring consistent nip pressure and uniform caliper, roll crown control plays a pivotal role in enhancing the overall performance of the papermaking process.
Next Steps for Improving Your Roll Crown Control
Improving roll crown control requires a proactive approach. Start by evaluating your current system and identifying areas for improvement. Consider investing in advanced technologies for more precise and automated control. Regular training for operators is also crucial for ensuring proper implementation and maximizing the benefits of effective roll crown control in your papermaking process.