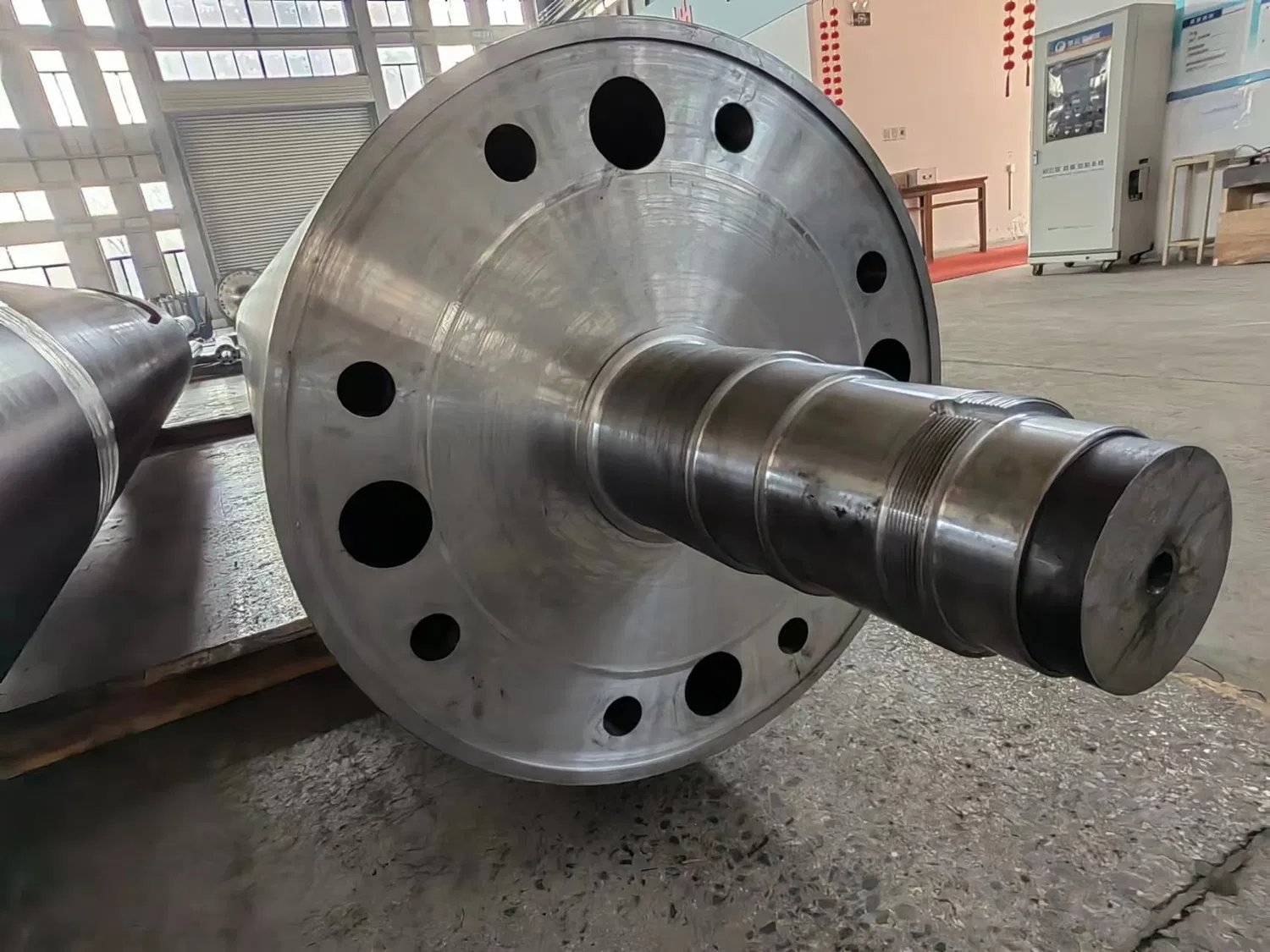
Paper manufacturing is a complex process involving numerous variables that influence the final product's quality. Among these, roll surface temperature plays a critical role, significantly impacting various paper properties. Understanding this relationship is essential for producing paper that meets specific requirements. This article delves into the intricacies of how roll surface temperature affects paper properties, providing practical insights for improved control and quality.
The Relationship Between Temperature and Smoothness
Roll surface temperature significantly influences paper smoothness. Higher temperatures generally lead to increased smoothness as the heat softens the paper fibers, allowing them to conform more readily to the roll surface during calendering. However, excessively high temperatures can cause issues like blackening or burning, negatively impacting the paper's appearance and structural integrity. Finding the optimal temperature balance is key to achieving the desired smoothness without compromising other properties.
Caliper and Temperature: A Delicate Balance
Caliper, or paper thickness, is also affected by roll surface temperature. Higher temperatures can lead to a slight reduction in caliper due to fiber compression. Conversely, lower temperatures can result in a thicker sheet. Controlling roll surface temperature is therefore crucial for maintaining consistent caliper and meeting specific product specifications. What are the ideal temperature ranges for different paper grades? This is a question that demands careful consideration of the desired caliper and other properties.
Temperature's Impact on Paper Strength
Roll surface temperature can indirectly influence paper strength. While not a direct determinant of tensile or tear strength, temperature variations can affect fiber bonding during the drying and calendering processes. Consistent temperature control throughout these stages helps ensure uniform fiber bonding, contributing to optimal strength properties.
The Role of Calendering and Temperature Control
Calendering is a critical process where paper is passed through a series of heated rolls to improve smoothness and gloss. Roll surface temperature during calendering plays a pivotal role in determining the final paper properties. Precise temperature control is vital for achieving the desired finish and avoiding defects. This often involves sophisticated control systems that monitor and adjust the temperature of each roll individually.
Troubleshooting Temperature-Related Issues
Variations in roll surface temperature can lead to several issues, including uneven caliper, surface defects, and inconsistent smoothness. Identifying and addressing these issues promptly is critical for maintaining product quality. Proper maintenance of the calendering rolls and accurate temperature monitoring systems are essential for preventing these problems.
Optimizing Temperature for Desired Paper Properties
Achieving specific paper properties requires careful control of roll surface temperature throughout the manufacturing process. This involves understanding the target properties and adjusting the temperature accordingly. Working with experienced operators and utilizing advanced process control systems can help optimize temperature profiles for consistent, high-quality paper production.
Practical Tips for Temperature Management
Implementing effective temperature management strategies is crucial for consistent paper quality. Regular calibration of temperature sensors, proactive maintenance of heating systems, and operator training on temperature control procedures are essential steps. Additionally, real-time temperature monitoring and data analysis can help identify potential issues before they impact the final product.
How Roll Surface Temperature Affects Coated Papers
Coated papers present unique challenges regarding temperature control. The coating layer is sensitive to temperature fluctuations, and improper temperatures can lead to coating defects, such as blistering or orange peel. Precise temperature control during the coating and drying processes is essential for achieving a smooth, uniform coating.
Future Trends in Temperature Control Technology
Advancements in temperature control technology are continuously improving the precision and efficiency of paper manufacturing. New sensor technologies, sophisticated control algorithms, and data analytics tools are enabling more precise temperature management, leading to enhanced paper quality and reduced waste.
Conclusion: Mastering Roll Surface Temperature for Optimal Paper Properties
How roll surface temperature impacts paper properties is a multifaceted topic with significant implications for paper manufacturers. By understanding the complex relationships between temperature and characteristics like smoothness, caliper, and strength, and by implementing effective temperature control strategies, manufacturers can achieve consistent, high-quality paper production. Consider conducting regular audits of your temperature control systems and operator training programs to ensure optimal performance and stay ahead of the curve. This proactive approach will lead to improved product quality and enhanced profitability in the long run.