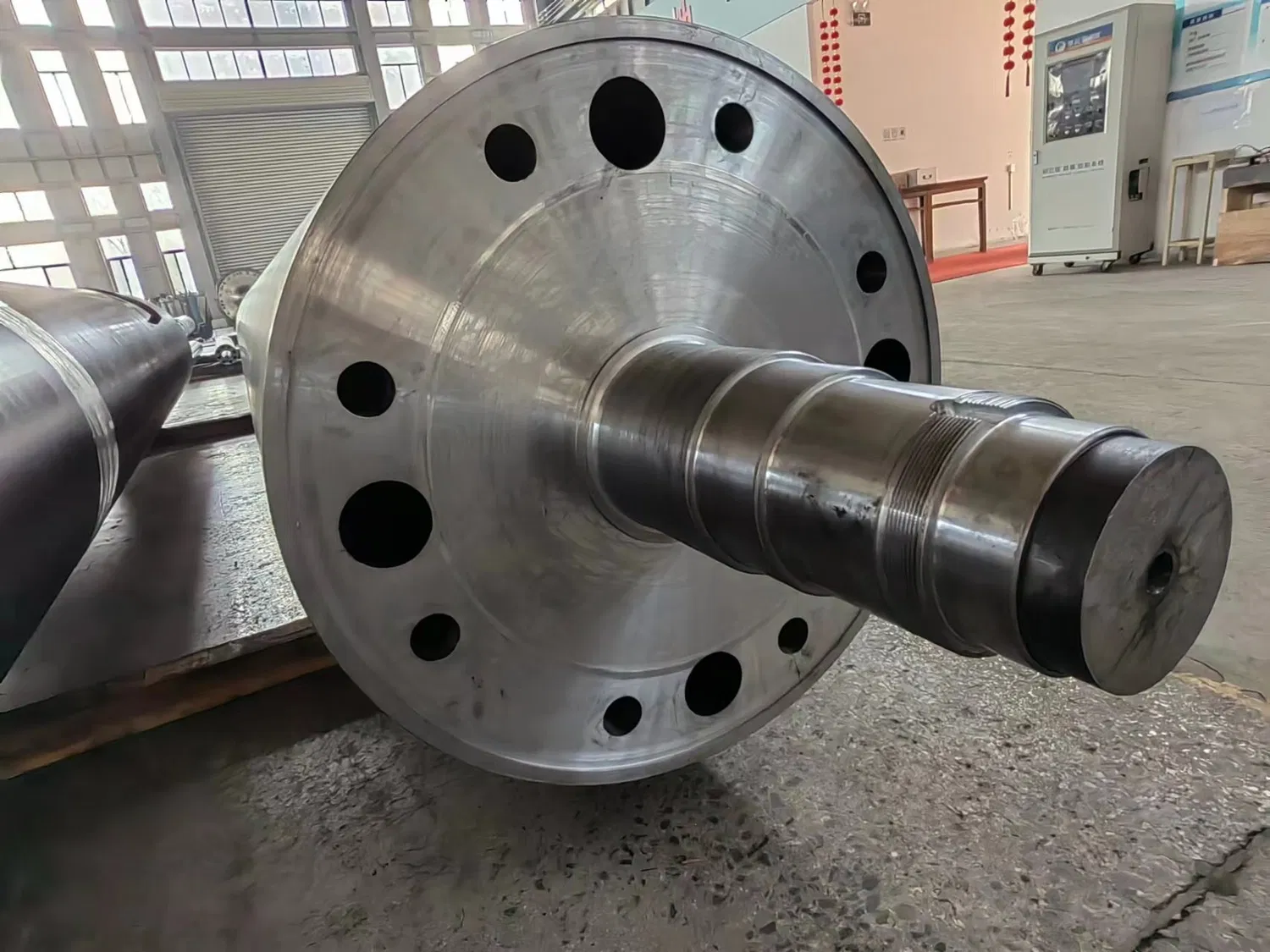
Roll covers, vital components in numerous industrial applications, are unfortunately prone to degradation. This deterioration can lead to significant operational inefficiencies and costly downtime. Understanding the root causes of **roll cover degradation** is the first step toward implementing effective preventative measures. This article will delve into the various factors that contribute to this issue, explore its detrimental effects, and provide actionable strategies for extending the lifespan of your roll covers. We’ll also consider factors like proper storage conditions and the impact of specific chemicals on rubber surfaces.
One of the most common culprits behind roll cover failure is chemical attack. Many industrial processes involve exposure to harsh chemicals, solvents, and oils. These substances can react with the elastomer material of the roll cover, causing it to swell, harden, crack, or even dissolve. The specific chemical resistance of a roll cover depends heavily on the type of elastomer used in its construction. Therefore, selecting the right material for your specific application is crucial. Are you aware of the chemical composition of the materials your rollers are exposed to? Matching the roll cover material to the chemical environment significantly reduces the risk of premature degradation.
Another significant factor contributing to **roll cover degradation** is mechanical wear and tear. Constant friction, abrasion, and impact forces can gradually erode the surface of the roll cover. This is especially prevalent in applications involving abrasive materials or high-speed operations. Factors like surface roughness of mating components, applied pressure, and the presence of foreign particles can all accelerate wear. Regular inspection for signs of wear, such as cuts, gouges, or excessive thinning, is crucial for identifying potential problems early on.
Heat, whether from the operating environment or generated by internal friction, can also wreak havoc on roll covers. Elevated temperatures can accelerate chemical reactions within the elastomer, leading to premature aging, hardening, and cracking. The maximum operating temperature varies depending on the specific elastomer, so it's essential to stay within the manufacturer's recommended temperature range. In applications where heat is unavoidable, consider using heat-resistant elastomers or implementing cooling systems to mitigate its effects. Proper cooling techniques can significantly prolong the life of the roll cover.
Environmental Factors and Their Impact on Roll Cover Life
Beyond chemical and mechanical stresses, environmental factors like ozone and UV radiation can also contribute to **roll cover degradation**. Ozone, a highly reactive form of oxygen, can cause cracking and surface deterioration, particularly in natural rubber and some synthetic elastomers. UV radiation from sunlight or artificial sources can also break down the polymer chains in the elastomer, leading to discoloration, embrittlement, and loss of flexibility. Shielding roll covers from direct sunlight and minimizing exposure to ozone are important preventative measures.
Improper storage can also significantly shorten the lifespan of roll covers, even when they're not in use. Storing roll covers in direct sunlight, near sources of heat, or in areas with high ozone concentrations can accelerate degradation. Ideally, roll covers should be stored in a cool, dry, and dark environment, away from chemicals and sharp objects. They should also be supported properly to prevent deformation or flat spots. Taking the time to properly store these expensive and vital parts pays off in the long run.
The effects of roll cover degradation can be far-reaching, impacting everything from product quality to production efficiency. A degraded roll cover can lead to uneven pressure distribution, inconsistent material handling, and ultimately, defects in the finished product. This can result in increased scrap rates, customer complaints, and ultimately, damage to your bottom line. Moreover, a failing roll cover can lead to unscheduled downtime for repairs or replacements, disrupting production schedules and increasing maintenance costs.
Preventative Measures and Maintenance Tips
Regular inspection and maintenance are key to preventing **roll cover degradation** and extending the lifespan of your industrial rollers. Establish a routine inspection schedule to check for signs of wear, damage, or chemical attack. Clean roll covers regularly with appropriate cleaning agents to remove contaminants and prevent the buildup of residue. Ensure proper alignment and tensioning of the rollers to minimize mechanical stress. Consider using protective coatings or wraps to shield roll covers from harsh environments. Investing in preventative measures will always be cheaper than replacing a damaged roller.
Furthermore, careful selection of the roll cover material is paramount. Understanding the specific operating conditions and potential stressors is essential for choosing the right elastomer. Consult with roll cover manufacturers or suppliers to determine the best material for your application. Factors like chemical resistance, temperature resistance, abrasion resistance, and hardness should all be considered. Don’t hesitate to ask for recommendations and material data sheets.
Finally, consider implementing a **rubber roller maintenance** program that includes regular inspections, cleaning, and preventative maintenance procedures. This program should be tailored to your specific operating conditions and the types of roll covers used in your facility. Training employees on proper handling and maintenance techniques can also significantly reduce the risk of damage and extend the lifespan of your roll covers. A well-designed program should include documented procedures and scheduled maintenance intervals.
What steps are you currently taking to prevent roll cover degradation in your facility? Implementing these proactive measures can save you time and money in the long run, ensuring the smooth and efficient operation of your industrial processes. Take action now to protect your investment and maximize the performance of your roll covers. Consider scheduling a consultation with a roll cover specialist for a comprehensive assessment of your needs and recommendations for optimal materials and maintenance practices.
```